joints mécaniquesjouent un rôle crucial dans la prévention des fuites pour de nombreuses industries. Dans l'industrie maritime, on trouvejoints mécaniques de pompe, des joints mécaniques d'arbre rotatif. Et dans l'industrie pétrolière et gazière, il existegarnitures mécaniques à cartouche,Les garnitures mécaniques à joint fendu ou à gaz sec. Dans l'industrie automobile, on trouve des garnitures mécaniques à eau. Dans l'industrie chimique, on trouve des garnitures mécaniques pour mélangeurs (garnitures mécaniques d'agitateurs) et des garnitures mécaniques pour compresseurs.
Selon les conditions d'utilisation, la solution d'étanchéité mécanique utilisée varie en fonction du matériau. De nombreux matériaux sont utilisés.joints d'arbre mécaniques tels que les joints mécaniques en céramique, les joints mécaniques en carbone, les joints mécaniques en carbure de silicone,Garnitures mécaniques SSIC etGarnitures mécaniques TC.
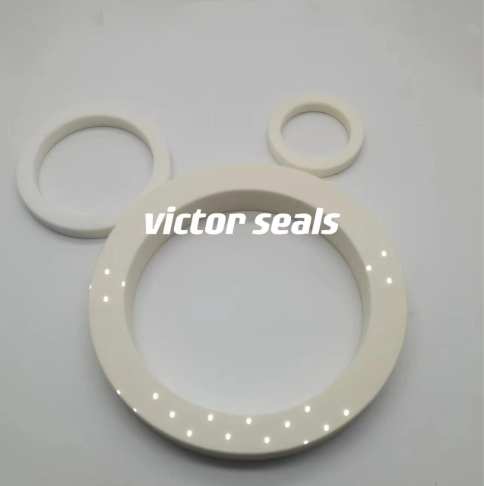
Garnitures mécaniques en céramique
Les garnitures mécaniques en céramique sont des composants essentiels dans diverses applications industrielles. Elles sont conçues pour empêcher les fuites de fluides entre deux surfaces, comme un arbre rotatif et un carter fixe. Ces joints sont très appréciés pour leur résistance exceptionnelle à l'usure, à la corrosion et aux températures extrêmes.
Le rôle principal des garnitures mécaniques en céramique est de préserver l'intégrité des équipements en prévenant les pertes de fluides ou la contamination. Elles sont utilisées dans de nombreux secteurs, notamment le pétrole et le gaz, la chimie, le traitement des eaux, l'industrie pharmaceutique et l'agroalimentaire. Leur utilisation répandue s'explique par leur construction durable ; elles sont fabriquées à partir de matériaux céramiques avancés offrant des performances supérieures à celles des autres matériaux.
Les garnitures mécaniques en céramique se composent de deux composants principaux : une face fixe (généralement en céramique) et une face rotative (généralement en graphite de carbone). L'étanchéité se produit lorsque les deux faces sont pressées l'une contre l'autre par la force d'un ressort, créant ainsi une barrière efficace contre les fuites de fluide. Pendant le fonctionnement de l'équipement, le film lubrifiant entre les faces d'étanchéité réduit les frottements et l'usure tout en maintenant une étanchéité parfaite.
Un facteur crucial qui distingue les joints mécaniques en céramique des autres types est leur résistance exceptionnelle à l'usure. Les matériaux céramiques possèdent d'excellentes propriétés de dureté qui leur permettent de résister aux conditions abrasives sans dommages importants. Il en résulte des joints plus durables qui nécessitent un remplacement ou un entretien moins fréquent que ceux fabriqués à partir de matériaux plus tendres.
Outre leur résistance à l'usure, les céramiques présentent également une stabilité thermique exceptionnelle. Elles peuvent supporter des températures élevées sans se dégrader ni perdre leur étanchéité. Elles sont donc parfaitement adaptées aux applications à haute température, là où d'autres matériaux d'étanchéité pourraient subir une défaillance prématurée.
Enfin, les garnitures mécaniques en céramique offrent une excellente compatibilité chimique et une résistance à diverses substances corrosives. Cela en fait un choix intéressant pour les industries qui manipulent régulièrement des produits chimiques agressifs et des fluides agressifs.
Les joints mécaniques en céramique sont essentielsjoints de composantsConçus pour prévenir les fuites de fluides dans les équipements industriels. Leurs propriétés uniques, telles que la résistance à l'usure, la stabilité thermique et la compatibilité chimique, en font un choix privilégié pour diverses applications dans de nombreux secteurs.
propriété physique de la céramique | ||||
Paramètre technique | unité | 95% | 99% | 99,50% |
Densité | g/cm3 | 3.7 | 3,88 | 3.9 |
Dureté | HRA | 85 | 88 | 90 |
Taux de porosité | % | 0,4 | 0,2 | 0,15 |
Résistance à la fracture | MPa | 250 | 310 | 350 |
Coefficient de dilatation thermique | 10(-6)/K | 5.5 | 5.3 | 5.2 |
Conductivité thermique | W/MK | 27,8 | 26,7 | 26 |
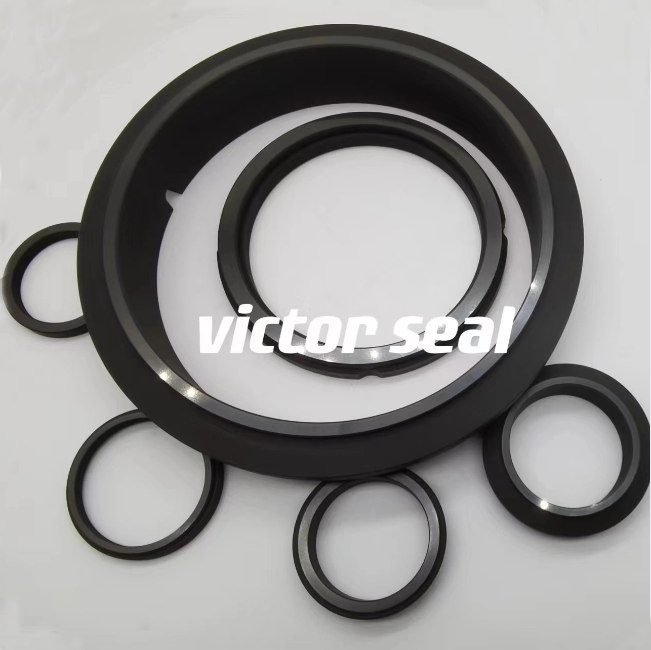
Garnitures mécaniques en carbone
Les joints mécaniques en carbone ont une longue histoire. Le graphite est une isoforme du carbone. En 1971, les États-Unis ont étudié avec succès un matériau d'étanchéité mécanique en graphite flexible, qui a permis de résoudre le problème de fuite des vannes à énergie atomique. Après un traitement approfondi, le graphite flexible devient un excellent matériau d'étanchéité, utilisé dans divers joints mécaniques en carbone pour l'étanchéité des composants. Ces joints mécaniques en carbone sont utilisés dans les industries chimiques, pétrolières et électriques, notamment pour l'étanchéité des fluides haute température.
Étant donné que le graphite flexible est formé par l'expansion du graphite expansé après une température élevée, la quantité d'agent intercalant restant dans le graphite flexible est très faible, mais pas complètement, de sorte que l'existence et la composition de l'agent intercalant ont une grande influence sur la qualité et les performances du produit.
Sélection du matériau de la face du joint en carbone
L'inventeur initial utilisait de l'acide sulfurique concentré comme oxydant et agent intercalant. Cependant, après application sur le joint d'un composant métallique, une faible quantité de soufre résiduelle dans le graphite flexible s'est avérée corroder le métal de contact après une utilisation prolongée. Face à ce problème, certains chercheurs nationaux ont tenté d'améliorer le graphite, comme Song Kemin, qui a préféré l'acide acétique et l'acide organique à l'acide sulfurique. L'acide nitrique, lent dans l'acide nitrique, et abaissé à température ambiante, est fabriqué à partir d'un mélange d'acide nitrique et d'acide acétique. En utilisant ce mélange comme agent d'insertion, le graphite expansé sans soufre a été préparé avec du permanganate de potassium comme oxydant, puis de l'acide acétique a été ajouté lentement à l'acide nitrique. La température a été ramenée à température ambiante, puis le mélange d'acide nitrique et d'acide acétique est obtenu. Le graphite lamellaire naturel et le permanganate de potassium sont ensuite ajoutés à ce mélange. Sous agitation constante, la température est de 30 °C. Après 40 minutes de réaction, l'eau est lavée jusqu'à neutralité et séchée à 50-60 °C. Le graphite expansé est ensuite obtenu après expansion à haute température. Cette méthode permet d'éviter la vulcanisation, à condition que le produit atteigne un certain volume d'expansion, ce qui assure une relative stabilité du matériau d'étanchéité.
Taper | M106H | M120H | M106K | M120K | M106F | M120F | M106D | M120D | M254D |
Marque | Imprégné | Imprégné | Phénol imprégné | Carbone d'antimoine (A) | |||||
Densité | 1,75 | 1.7 | 1,75 | 1.7 | 1,75 | 1.7 | 2.3 | 2.3 | 2.3 |
Résistance à la fracture | 65 | 60 | 67 | 62 | 60 | 55 | 65 | 60 | 55 |
Résistance à la compression | 200 | 180 | 200 | 180 | 200 | 180 | 220 | 220 | 210 |
Dureté | 85 | 80 | 90 | 85 | 85 | 80 | 90 | 90 | 65 |
Porosité | <1 | <1 | <1 | <1 | <1 | <1 | <1,5 | <1,5 | <1,5 |
Températures | 250 | 250 | 250 | 250 | 250 | 250 | 400 | 400 | 450 |
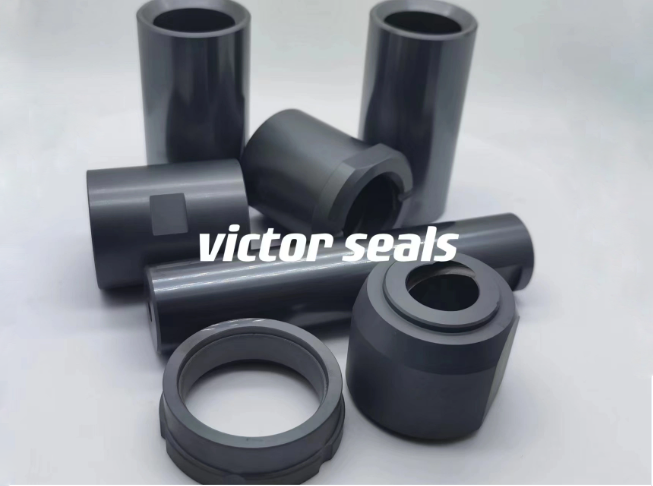
Garnitures mécaniques en carbure de silicium
Le carbure de silicium (SiC), également appelé carborundum, est composé de sable de quartz, de coke de pétrole (ou de coke de charbon), de copeaux de bois (qui doivent être ajoutés à la production de carbure de silicium vert), etc. Le carbure de silicium contient également un minéral rare dans la nature, le mûrier. Parmi les matières premières réfractaires modernes de haute technologie non oxydées, le carbure de silicium est l'un des matériaux les plus utilisés et les plus économiques, appelé sable d'acier doré ou sable réfractaire. Actuellement, la production industrielle chinoise de carbure de silicium se divise en carbure de silicium noir et carbure de silicium vert, tous deux des cristaux hexagonaux d'une proportion de 3,20 à 3,25 et d'une microdureté de 2 840 à 3 320 kg/m².
Les produits en carbure de silicium sont classés en plusieurs catégories selon les environnements d'application. Il est généralement utilisé en mécanique. Par exemple, le carbure de silicium est un matériau idéal pour les garnitures mécaniques en carbure de silicium en raison de sa bonne résistance à la corrosion chimique, de sa grande résistance mécanique, de sa dureté élevée, de sa bonne résistance à l'usure, de son faible coefficient de frottement et de sa résistance aux températures élevées.
Les bagues d'étanchéité SIC se divisent en bagues statiques, bagues mobiles et bagues plates, etc. Le silicium SiC peut être transformé en divers produits en carbure, tels que bagues rotatives, sièges fixes et bagues en carbure de silicium, selon les exigences spécifiques des clients. Il peut également être utilisé en combinaison avec du graphite. Son coefficient de frottement est inférieur à celui de la céramique d'alumine et des alliages durs, ce qui lui permet d'être utilisé à des valeurs PV élevées, notamment en conditions d'acides et de bases forts.
La réduction des frottements du SIC est l'un des principaux avantages de son utilisation dans les garnitures mécaniques. Le SIC résiste donc mieux à l'usure que d'autres matériaux, prolongeant ainsi la durée de vie du joint. De plus, la réduction des frottements du SIC réduit les besoins en lubrification. L'absence de lubrification réduit les risques de contamination et de corrosion, améliorant ainsi l'efficacité et la fiabilité.
Le SIC présente également une excellente résistance à l'usure. Il peut donc supporter une utilisation continue sans se détériorer ni se casser. Il est donc idéal pour les applications exigeant un haut niveau de fiabilité et de durabilité.
Il peut également être rodé et poli, permettant ainsi de rénover un joint plusieurs fois au cours de sa durée de vie. Il est généralement utilisé dans des applications mécaniques, notamment dans les garnitures mécaniques, pour sa bonne résistance à la corrosion chimique, sa grande résistance mécanique, sa dureté élevée, sa bonne résistance à l'usure, son faible coefficient de frottement et sa résistance aux températures élevées.
Utilisé pour les surfaces des garnitures mécaniques, le carbure de silicium améliore les performances, prolonge la durée de vie des garnitures et réduit les coûts de maintenance et d'exploitation des équipements rotatifs tels que les turbines, les compresseurs et les pompes centrifuges. Les propriétés du carbure de silicium varient selon son mode de fabrication. Le carbure de silicium lié par réaction est formé par la liaison de particules de carbure de silicium entre elles lors d'un processus de réaction.
Ce procédé n'affecte pas significativement la plupart des propriétés physiques et thermiques du matériau, mais il limite sa résistance chimique. Les produits chimiques les plus fréquemment problématiques sont les caustiques (et autres produits chimiques à pH élevé) et les acides forts ; par conséquent, le carbure de silicium lié par réaction ne doit pas être utilisé pour ces applications.
Fritté par réaction infiltréCarbure de silicium. Dans ce matériau, les pores du carbure de silicium d'origine sont comblés par infiltration par combustion du silicium métallique, ce qui produit du SiC secondaire et lui confère des propriétés mécaniques exceptionnelles, le rendant ainsi résistant à l'usure. Grâce à son retrait minimal, il peut être utilisé pour la production de pièces de grandes dimensions et complexes, avec des tolérances serrées. Cependant, la teneur en silicium limite la température maximale de fonctionnement à 1 350 °C et la résistance chimique à un pH d'environ 10. Ce matériau n'est pas recommandé pour une utilisation en environnements alcalins agressifs.
Frittéle carbure de silicium est obtenu par frittage d'un granulé de SIC très fin pré-comprimé à une température de 2000 °C pour former des liaisons solides entre les grains du matériau.
Tout d'abord, le réseau s'épaissit, puis la porosité diminue, et enfin les liaisons entre les grains se frittent. Ce processus entraîne un retrait important du produit, d'environ 20 %.
Bague d'étanchéité SSIC Il résiste à tous les produits chimiques. Sa structure étant exempte de silicium métallique, il peut être utilisé à des températures allant jusqu'à 1 600 °C sans altérer sa résistance.
propriétés | R-SiC | S-SiC |
Porosité (%) | ≤0,3 | ≤0,2 |
Densité (g/cm3) | 3.05 | 3.1~3.15 |
Dureté | 110~125 (HS) | 2800 (kg/mm2) |
Module d'élasticité (Gpa) | ≥ 400 | ≥410 |
Teneur en SiC (%) | ≥ 85 % | ≥ 99% |
Teneur en Si (%) | ≤15% | 0,10% |
Résistance à la flexion (Mpa) | ≥350 | 450 |
Résistance à la compression (kg/mm2) | ≥ 2200 | 3900 |
Coefficient de dilatation thermique (1/℃) | 4,5×10-6 | 4,3×10-6 |
Résistance à la chaleur (dans l'atmosphère) (℃) | 1300 | 1600 |
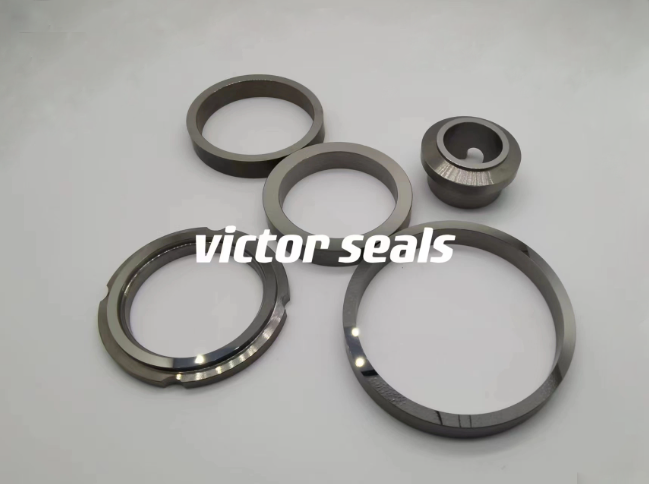
garniture mécanique TC
Les matériaux TC se caractérisent par une dureté, une résistance mécanique et une résistance à l'abrasion et à la corrosion élevées. On les appelle « dents industrielles ». Grâce à leurs performances supérieures, ils sont largement utilisés dans l'industrie militaire, l'aérospatiale, l'usinage, la métallurgie, le forage pétrolier, les communications électroniques, l'architecture et d'autres domaines. Par exemple, dans les pompes, les compresseurs et les agitateurs, les bagues en carbure de tungstène sont utilisées comme garnitures mécaniques. Leur bonne résistance à l'abrasion et leur dureté élevée en font des matériaux idéaux pour la fabrication de pièces résistantes à l'usure, aux températures élevées, au frottement et à la corrosion.
Selon sa composition chimique et ses caractéristiques d'utilisation, le TC peut être divisé en quatre catégories : tungstène-cobalt (YG), tungstène-titane (YT), tungstène-titane-tantale (YW) et carbure de titane (YN).
L'alliage dur tungstène-cobalt (YG) est composé de WC et de Co. Il convient au traitement de matériaux cassants tels que la fonte, les métaux non ferreux et les matériaux non métalliques.
La stellite (YT) est composée de WC, TiC et Co. L'ajout de TiC à l'alliage améliore sa résistance à l'usure, mais diminue sa résistance à la flexion, ses performances de meulage et sa conductivité thermique. En raison de sa fragilité à basse température, elle est uniquement adaptée à la coupe à grande vitesse de matériaux courants et non à l'usinage de matériaux cassants.
Du tungstène-titane-tantale (niobium)-cobalt (YW) est ajouté à l'alliage pour augmenter la dureté à haute température, la résistance mécanique et la résistance à l'abrasion grâce à une quantité appropriée de carbure de tantale ou de niobium. Parallèlement, la ténacité est améliorée et les performances de coupe globales sont améliorées. Cet alliage est principalement utilisé pour les matériaux durs et les coupes intermittentes.
L'alliage à base de titane carbonisé (YN) est un alliage dur composé de TiC, de nickel et de molybdène. Il présente les avantages suivants : dureté élevée, propriétés anti-adhérence, résistance à l'usure progressive et résistance à l'oxydation. Il est usinable à des températures supérieures à 1 000 degrés. Il est applicable à la finition continue des aciers alliés et à la trempe de l'acier.
modèle | teneur en nickel (% en poids) | densité (g/cm²) | dureté (HRA) | résistance à la flexion (≥N/mm²) |
YN6 | 5.7-6.2 | 14,5-14,9 | 88,5-91,0 | 1800 |
YN8 | 7.7-8.2 | 14,4-14,8 | 87,5-90,0 | 2000 |
modèle | teneur en cobalt (% en poids) | densité (g/cm²) | dureté (HRA) | résistance à la flexion (≥N/mm²) |
YG6 | 5,8-6,2 | 14,6-15,0 | 89,5-91,0 | 1800 |
YG8 | 7,8-8,2 | 14,5-14,9 | 88,0-90,5 | 1980 |
YG12 | 11,7-12,2 | 13,9-14,5 | 87,5-89,5 | 2400 |
YG15 | 14,6-15,2 | 13,9-14,2 | 87,5-89,0 | 2480 |
YG20 | 19,6-20,2 | 13,4-13,7 | 85,5-88,0 | 2650 |
YG25 | 24,5-25,2 | 12,9-13,2 | 84,5-87,5 | 2850 |